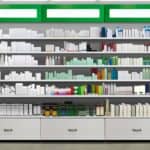
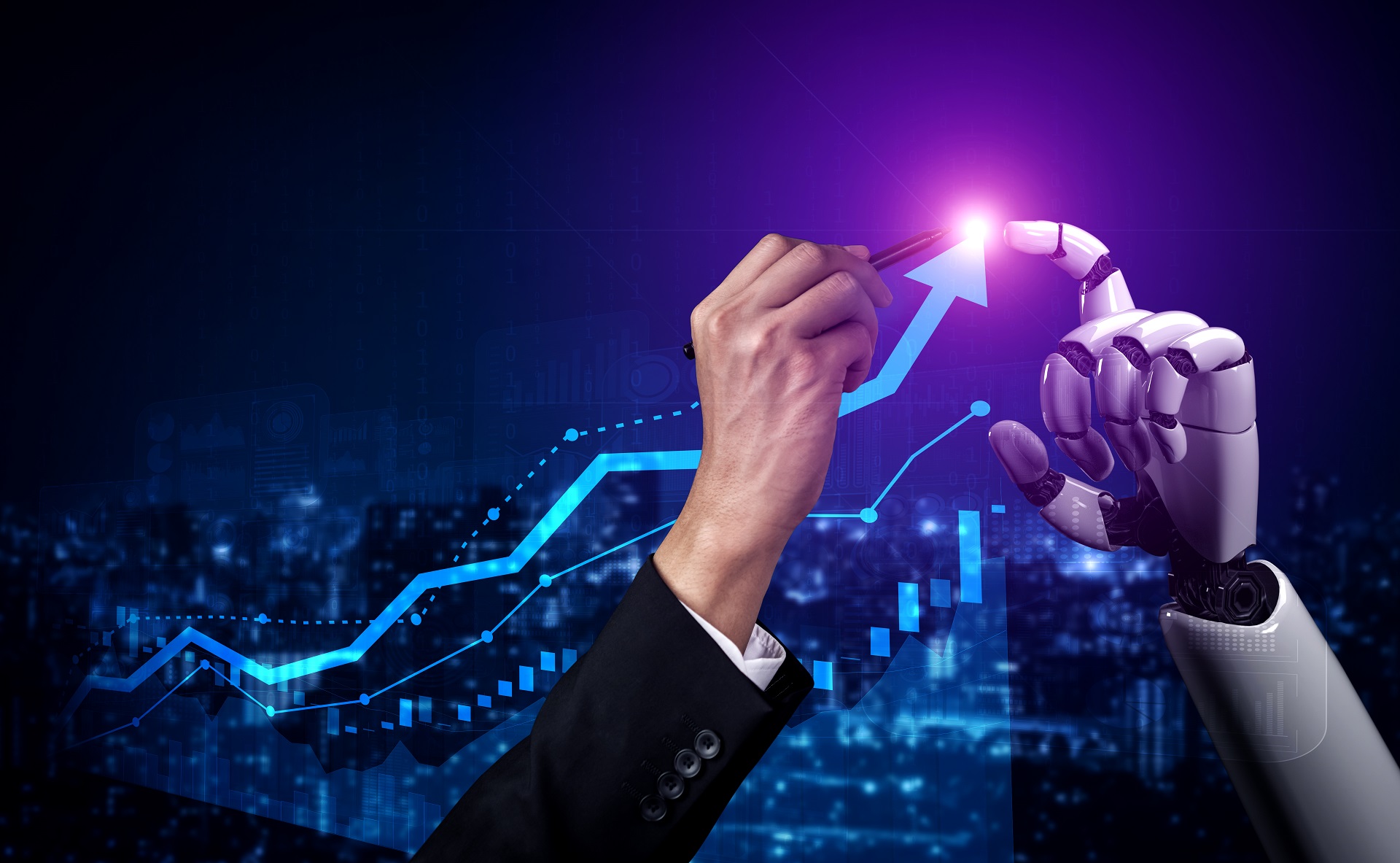
What happens when you do them without a WMS to help with warehouse activity management?
Well, first of all, it’s very time-consuming (and nerve, I might add). When you see a truck full of goods coming in and you know you have to stand there and check, count and visually inspect all the goods, it’s a bit of a drag. And not just to you, but also to the other warehouse operators who help with checking and unloading the goods.
Of course, you want everything to happen quickly and properly because the next truck will be here soon. Or because your warehouse operators have other things to do. However, if there is no quality WMS in place, the whole goods receipt can turn into a total fiasco.
Please, let me explain By now we have already established that freight receipts without WMS are time consuming. Way too much time. But this is just the tip of the iceberg.
The biggest problem of receipts without WMS is that many errors occur. On one side, checking the goods by counting and visual inspection is automatically subject to errors.
It’s hard as a human being to keep a constant eye out to see that some products that look identical or very similar are different products, especially if only one digit/letter differs from the barcode.
And that’s where the fun begins. These stocks will be wrongly entered into the management system or ERP, and then you discover that for one of the products you don’t have stock, although you should, and customers start complaining that they got the wrong products in their orders.
And if we also talk about the FMCG area, where there are perishable products, there is a need to be very careful about traceability, expiry dates and batch numbers.
Solving all these problems such as too much time wasted, errors and traceability of goods can be solved simply with a WMS and a terminal that scans product barcodes.
For example, the Warehouse Manager WMS developed by Transart in addition to being integrated with the ERP so that stocks scanned with the WMS terminal go directly to management. The WMS can also work with complex GS1-128 barcodes, which also integrates the expiry date and batch number.
Plus you have flexibility. You can make guided receipts, i.e. check the goods from the supplier on the basis of the invoice or the accompanying goods note. And if you want, you can also start making unguided receipts and later enter the invoice from the supplier into the ERP system.
Once the goods received from suppliers have been received and checked, it’s time to store them on the warehouse shelves. To avoid chaotic storage, the warehouse must be organised by location.
A good WMS has developed a functionality called Warehouse Map. It helps you in several ways:
Most companies store the same goods in the same place of the warehouse every time in order to be found more easily, and the warehouse map helps in this situation.
We discussed picking slightly above, but this activity of picking goods from the warehouse also deserves its own separate section on the ramp. Things here are simple, if the picking, checking and preparation of the goods is done correctly, then the exact products requested by the customers will be delivered. Otherwise there will be arguments, annoyances and additional costs for all parties involved.
To avoid such problems, the Transart WMS takes into account several criteria such as delivery dates, weekend days, blocked stock or delivery routes, and picking is guided by delivery/loading notices.
Another important operation that takes place in a warehouse is the handover of goods for delivery. There can be a lot of confusion here, especially if there are several similar products in the warehouse. That’s why mobile terminals that scan barcodes help operators make sure they have the right products ready for each customer’s order. Basically the WMS warns operators that they are adding the wrong products to a particular order.
The Transart WMS notifies people in the warehouse to prepare the goods according to the delivery date on the proforma in order to ensure compliance with the delivery terms agreed with the customers.
Anyone who has done an inventory count manually knows how long the process takes, how exhausting it is, and how likely it is to make mistakes during the process.
A WMS greatly simplifies all the inventory work, so you end up with a quick, easy and accurate inventory, which is what we all want.
For example, using the Transart WMS you can do inventory with several people at once. You offer them terminals with which they can scan barcodes on products, you divide them up into different areas of the warehouse/showroom/store, and then in the WMS the scanned goods are automatically accumulated from all operators. No more sitting around collecting and looking to validate all sorts of verification keys.
Another practical issue is partial inventory. This functionality is useful if you don’t have time to do a total inventory or if you don’t want to do one because it would mean closing the store/warehouse and losing sales. Basically, when you do a partial inventory, you can choose only a specific area of the warehouse in which to do this activity.
For FMCG, with the Transart WMS you can also do inventory on the side of batch series and expiry dates because most of the time in this industry we are talking about perishable products.
In the case of warehouses which sell products with variable weight, it is necessary to use scales integrated with the WMS system.
For example, with Warehouse Manager WMS you can integrate multiple weighing, and if you need to weigh the same type of product several times for a single order, the WMS will automatically add up the quantities at the end. For suppliers of meat products, the Transart WMS also manages the weight loss (shrinkage) that occurs during the transport of meat to the final customer.
A WMS is also useful for showroom stores, where customers need personalized assistance in choosing the products they need. Let’s take an example from the bricolage/building materials area.
The customer comes into the showroom and needs all kinds of products and information. In this case, a sales consultant in the showroom can walk the customer through the shelves and show them what materials and tools they need. And the products that the customer has decided to buy are scanned by the consultant and finally this information is sent to invoicing. Once the proforma invoice is ready, it goes to the warehouse and the order starts to be prepared for delivery.
For situations where customers return products, the Transart WMS greatly simplifies the process. Basically in the WMS you enter the quantity of returned products, and then the system automatically searches for the data, and then generates the return invoice from the ERP.
At the same time, the WMS is a useful tool for transferring goods from the warehouse to the store with the help of transfer notices or vouchers that are automatically created by the program.
Another thing the WMS can be used for is printing various output documents such as: custody notice, transfer notice, invoice or accompanying goods notice or even product information.
Scanners can be used to quickly check the price of a product, both to answer a customer’s question when making a consultative sale in the showroom and to check whether the price on the shelf is the same as the price displayed by the WMS.
In addition to pricing, barcode scanners can be used to quickly check what stock levels are available for a particular product.
If you want to learn more about the WMS system developed by Transart, contact us with confidence and talk to an expert about how this system can be helpful for your warehouse.
Subscribe to our Newsletter
No spam, only notifications and updates about Transart products and services.
Social Media
News
Testimonial Video